Expert Metal Stamping Services for Precision Manufacturing Solutions
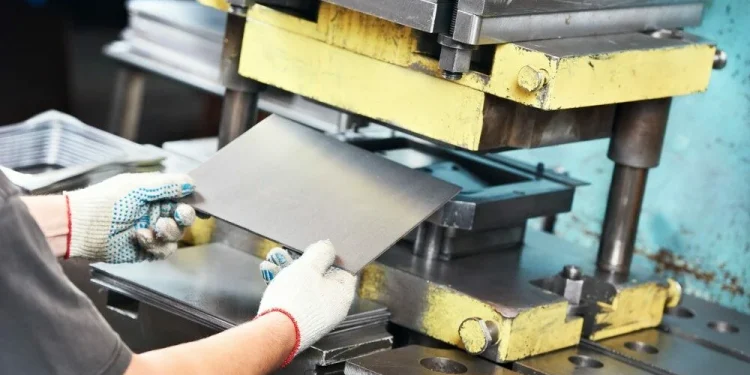
Precision is the cornerstone of successful manufacturing, and expert metal stamping services are key to achieving it. From intricate designs to high-volume production, metal stamping offers the accuracy and efficiency modern industries demand. Whether you need custom components or reliable mass production, these services provide tailored solutions for your unique requirements. Discover how expert metal stamping services can elevate your manufacturing process and deliver superior results.
The Art of Metal Stamping: A Fusion of Science and Creativity
Metal stamping is a combination of engineering precision and artistic creativity is a manufacturing process used in mass production where complex parts can be made from plenty of sheets of different parts of various materials. This process uses specialized dies to convert sheets of metal into near-final shape and can accomplish this efficiently and precisely. Even so, this strange concoction of science and art has come a long way over the years, growing more sophisticated and allowing for more imagination in design.
The Historical Evolution of Metal Stamping Techniques
Metal stamping has a long history that dates back centuries to ancient times where craftsmen manually manufactured complex metal objects. With industrial revolution and scientific developments the methods of metal stamping enhanced with time. The 19th century was an important milestone in the history of stamping, with mechanized stamping machines allowing for increased accuracy and efficiency leading to faster production. With the introduction of punch presses and progressive dies early in the 20th century, companies started to adopt them as their means of manufacturing in an even more efficient manner. PowerPress – Modern metal stamping today utilizes silent CNC technology that provides unmatched accuracy, and can manufacture complex geometry that was once limited only to handcrafted models.
Understanding the Role of Technology in Modern Metal Stamping
Technology is essential in the metal stamping services in a modern world, allowing to solve the hindrances that have been around for decades. This can be avoided by using advanced software programs where the engineers can design and also simulate the whole manufacturing process even before manufacturing begins, reducing the errors and making sure that each die is customized to achieve the best results. Moreover, laser cutting is a game changer here too, because it offers cleaner caul as well as lesser wastage in comparison to the old methods of handling the materials. With the help of robotics and automation, productivity has increased even higher, performing mundane tasks quickly and accurately while transferring higher management issues to human operators. Utilization of technology within this process does not only enhance production efficiency, but also rise the standards of end products quality.
Expert Insights: What Makes a Great Metal Stamping Professional?
A qualified metal stamping professional also has a wide configuration of skills, which includes experience with both technical knowledge and inventive problem-solving capabilities. Their experience in metallurgy, materials science, and engineering principles enable them to appropriately select which materials and processes are best suited for each project. Moreover, it helps them troubleshoot issues in real-time and implement creative solutions that improve product quality and efficiency. Other than that, a great professional also has communication; they aim to work with their clients and understand their requirements and then implement those requirements in a viable and cost-effective solution to the manufacturing process. A top metal stamping areesian in today adaptive technological world is someone who engages in continuous education and stays abreast of the latest trends.
Precision at Its Finest: Why Quality Control Matters
When it comes to metal stamping, precision is not a necessity but the heart beat of your manufacturing project. Given that even a slight error can have dire consequences in other production processes or customer health and safety, QC is paramount in this field.
Critical Quality Assurance Processes in Metal Stamping
Metal stamping quality assurance features an array of stringent processes aimed at capturing defects prior to the final product. The first step in that direction is checking raw materials: they need to be fully compliant with all specifications before they ever reach the production line. During the stamping process itself, regular sampling and in-line inspections can identify defects due to wear and tear of the equipment, variability of material properties, etc. Today, many systems include statistical process control (SPC) methods that verify real-time production data that help manufacturers quickly make corrections when things are not right. In the end, an effective quality assurance process is critical not just for regulatory compliance but also for retaining end-user confidence and brand equity.
How Advanced Equipment Enhances Product Reliability
New machinery and equipment in metal stamping have improved the quality of the finished product significantly. Modern stamping presses with a high performant setup have the ability to hold tighter tolerances than ever before with consistent results. For example, functions like automatic feed systems and monitoring tools in real-time allow changes to be made easily and quickly during production, which guarantees that quality is paramount during the manufacturing process. In addition to this, die design capabilities now can provide complication in the design, thanks to the advanced methods related to die design, such techniques include solid modeling software that gives clear image and better fit of end product. By focusing on equipment, it guarantees a better ROI since it lessens the chances of defects and increases the overall efficiency of production.
Real-World Case Studies: The Impact of Quality Control Flaws
Quality control mishaps can be both dramatic and expensive — a type of cautionary tale in the metal stamping industry. In an example related to an auto parts manufacturer in which poor quality assurance processes were ignored, the manufacturer was forced to recall vehicles due to a defect in a batch of stamped components, resulting in substantial costs and harming the brand. The other example is of an aerospace firm, which had to rework upon finding out certain components for aircraft engines had been manufactured which did not meet stringent quality standards. The above cases demonstrate how focused we must be towards quality in metal stamping not only from the start, with no cracks in the process but also how lives can get impacted if one does not maintain the quality standard.
Tailored Solutions: Custom Metal Stamping for Unique Industries
In a world where industries demand unique solutions, custom metal stamping has become crucial for meeting specific requirements across various sectors. Whether it’s automotive, aerospace, or electronics, each industry has its particularities that necessitate tailored metal stamping approaches.
Exploring Industry-Specific Requirements: Automotive, Aerospace, and Beyond
High-volume parts production is common in the automotive industry involving parts such as brackets, housings, and connectors that require precision-engineered components. The incorporation of sophisticated technologies in Vehicles makes them more complex, therefore, demands the need for Custom Metal Stamping Solutions which passes the rich issue of safety and also performance parameters. Lightweight materials and tighter tolerances are critical components for the aerospace space, as they can directly affect factors like flight safety and fuel efficiency. The these parts can be made with techniques like CNC machining combined with metal stamping that are compliant with aerospace standards; however, we can use materials such as aluminum and titanium for high performance. Outside of these prescriptive areas, electronics is requiring complex stampings for components such as heat sinks and connector housings with tight electrical requirements.
Design Innovation: Collaborating with Clients for Tailored Solutions
Metal stamping experts and customers work together to come up with creative designs for specific needs. By engaging manufacturers from the beginning, clients will be able to provide detailed information on their design intentions, functional requirements, and aesthetics that manufacturers can leverage to drive customized designs that also control for production techniques. Advanced modeling software allows designers and engineers to work together to iterate and rapidly prototype solutions based on client input. By using an iterative strategy, manufacturers can experiment with advanced designs that provide clients a competitive edge in their industry.
Environmental Considerations: Sustainable Practices in Metal Stamping
With many industries turning to more sustainable and responsible practices, metal stamping is not exempt. Green process is not just scientists but manufacturers are also adopting this process where they keep the process working with minimum waste and energy usage. This involves recycling the scrap metal that occurs during production, utilizing energy-efficient machines and researching other alternative materials that have lesser environmental impact. In addition, sustainability-minded architects guide clients to specify materials that not only suit their functional requirements but also fulfill their sustainability objectives. Metal stamping professionals are also part of this trend — one that sees an uplift in realization what the future of sustainability may look like — embracing a holistic approach that goes beyond compliance to achieve positive outcomes and social marketing benefits by responding to the needs of environmentally and socially responsible consumers and businesses.
The Future of Metal Stamping: Trends and Technologies to Watch
As we move forward, the metal stamping industry is set for a revolution, with innovations geared towards improving efficiency, quality, and sustainability. Stakes have to be managed; key trends and emerging technologies are redefining the manner in which manufacturers are approaching metal stamping and using them for their benefit.
Automation and Robotics: Revolutionizing the Stamping Process
Metal stamping automation and robotics are taking the manufacturers’ operation to the next level. Automation helps businesses minimize human error and produce at higher speeds to meet their growing demands without compromising quality. Powerful robotic arms are good at repetitious jobs like loading and unloading materials, but human users can now track complex workflows and make decisions. In addition, automated production can also enable just in time production models that minimize inventory costs and waste as production can be closely matched to exact market demand. But switching to fully realized automation requires new technologies and reworking how the workforce is trained to work around automation.
AI and Machine Learning: Predictive Maintenance in Metal Stamping
Metal stamping companies are finding ways AI and machine learning are influencing their predictive maintenance strategies. Using historical production data along with actual machine performance, AI algorithms can predict equipment failures before they happen, allowing for proactive measures to minimize downtime and maintenance costs. This enables a higher level of transparency in operations, as stakeholders are able access data-backed visibility to performance indicators and potential areas for improvement. With manufacturers harnessing the power of these technologies, not only will operational efficiency be enhanced but the overall product quality.
The Rising Demand for Lightweight Materials: Challenges and Opportunities
Across industries — from aerospace, it is more relevant to automotive — there is a focus on lightweighting, which creates challenges, but also opportunities for metal stamping. In the pursuit to enhance efficiency and performance, echo products of stamping solutions compatible with emerging materials such as advanced high-strength steels (AHSS) and composites with new tools. But doing so demands equipment upgrades and new dies customized to process these materials, which means both capital and research must make a transition to ensure that processing is viable. Moreover, producers who specialize in metal stamping must be willing to remain abreast of advances in the science of material and a responsive challenge with respect to technology advancements. And in the long run, it will be crucial for the metal stamping industry to remain competitive, especially in the face of continuously changing technology to both address the needs of modern industries, but also to continue creating the innovation and progress necessary to keep the industry moving forward.